New Ulm resident Pegeen Rozeske was visiting Jack McGowan’s annual History Fest event at Land of Memories Park in 2001 when she ran into a friend—with a problem. Her friend was a historical reenactor, and he had a hole in his shoe.
“I grabbed him by the left hind leg and patched his shoe,” recalled Rozeske, who had been dabbling in leatherwork for several years at this point. “He said, ‘Well, if you can patch them, you can make them.’ That sparked something.”
Now, Rozeske has a full-time business, Pegeen Rozeske Custom Leather. While she focuses on creating custom shoes, she also repairs shoes and creates many other leather items, from purses to belts. The bulk of her work is done with traditional methods, including hand-sewing and hand-tooling designs, since a large portion of her customers are historical reenactors.
He said, ‘Well, if you can patch them, you can make them.’ That sparked something.Pegeen Rozeske
Rozeske is a historical reenactor herself, and she teaches thousands of elementary students about leatherworking every year at different events like History Fest and Big Island Rendezvous in Albert Lea.
“I enjoy it all,” Rozeske said. “You put leather in my hand, and I’m happy.”
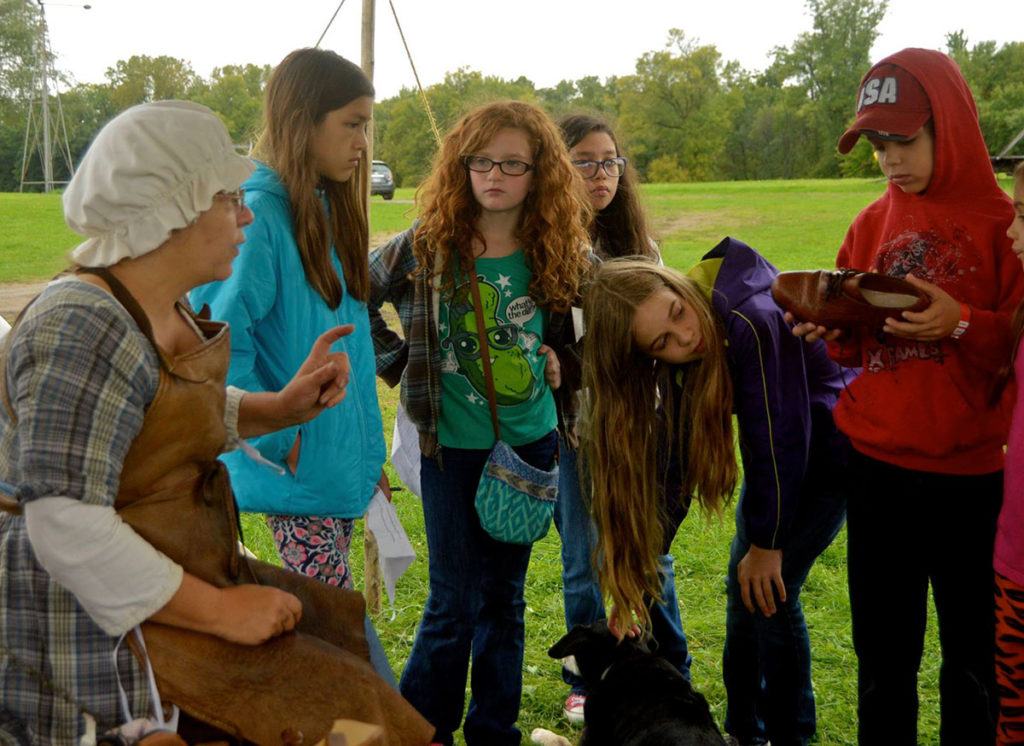
A winding road
Growing up on a farm in Bernadotte township, near New Ulm, Rozeske said there were “a lot of things” she wanted to be when she grew up—but she wasn’t always encouraged in her dreams.
“They were always shot down because I was small or I was a girl,” she recalled. “I grew up in an era when [a girl] couldn’t be things like firefighters or police officers.”
While Rozeske was interested in everything from music to animal husbandry, she ended up studying civil engineering at what is now South Central College in Mankato. After graduating, she found a job with Minnesota’s Department of Transportation, designing roads.
While Rozeske said many people work for the DOT for 40 years or more, there was “a change in the air” after she had been there for 19 years.
“They were laying people off left and right,” she said. “I took the opportunity to study [shoemaking].”
Rozeske explained that the idea came to her after years of cultivating her interest in leatherwork. She had started when her children were young, creating “mostly useful” items such as sheaths for her husband’s hunting guns and purses for herself.
When you go to a school and learn something, sometimes [it doesn’t connect] until you actually have to work with it.Pegeen Rozeske
“I love leather,” she said. “I started it because you use a hammer and pound out things. I gave me something other than my children to pound on—it was great stress relief!”
After her friend at History Fest recommended that she look into shoemaking, Rozeske started to do some digging and found the Honorable Cordwainers’ Company, a nonprofit educational organization that was all about shoemaking. Through them, she was able to connect with master bootmaker D.W. Frommer, who has been making custom tailored boots and shoes in Redmond, Oregon for more than 40 years.
Frommer was offering a boot-making workshop on the west coast, and Rozeske decided to go for it. She spent several weeks with Frommer in the fall of 2003, learning everything from how to measure a foot to how to operate the machinery connected with shoemaking.
“I learned so much from him, and I’m still learning,” she said. “When you go to a school and learn something, sometimes [it doesn’t connect] until you actually have to work with it, and you go, ‘Oh, yeah, he said something about that way back when…’ It triggers it. You didn’t know you learned it, but you did, and then you just have to remember it.”
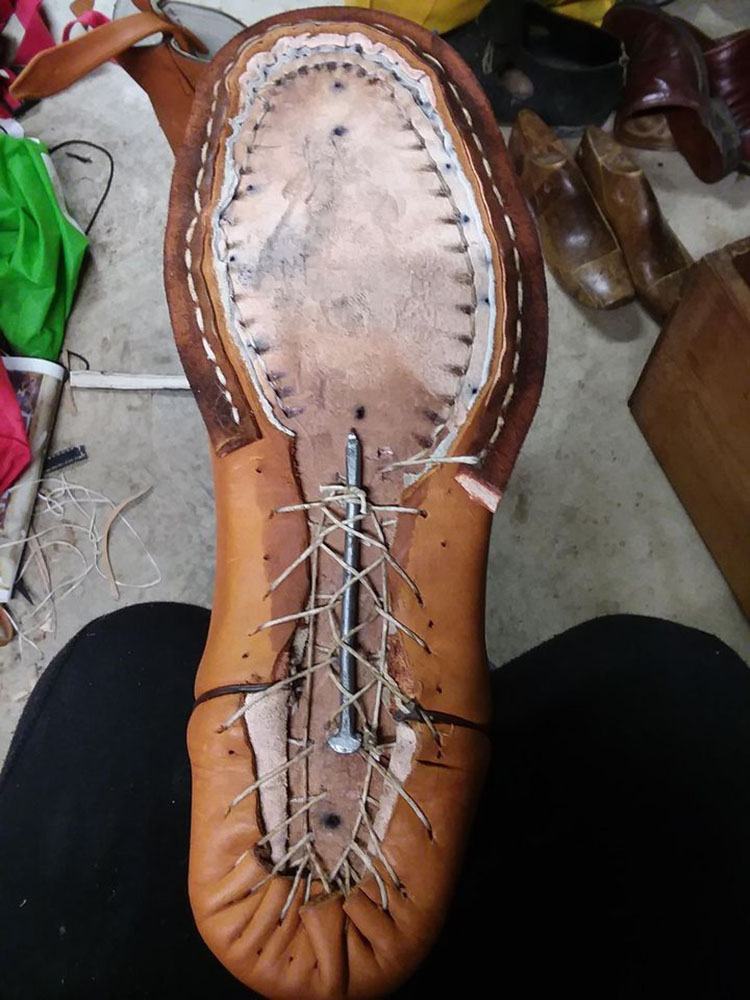
Old school style
After Rozeske learned the basics of shoemaking, she came back to Minnesota to start herself. However, what took three weeks at Frommer’s workshop took Rozeske quite a bit longer, since she didn’t have nearly as high-tech equipment as he did.
“He had machines [like stitching machines] and big sewing machines,” Rozeske said. “I got back [to Minnesota], and I had … a knife. A hammer. A couple small tools. But he said if you have a knife and a fork, you can make a boot.”
They were making shoes and boots long before they had machines. I started researching that. And I took that knowledge and started making handmade shoes.Pegeen Rozeske
To make up for her lack of equipment, Rozeske started researching historic methods for creating boots and shoes. She reached out to groups such as Colonial Williamsburg, a living history museum in Virginia, as well as several other east coast historical museums.
“They were making shoes and boots long before they had machines,” she said. “I started researching that. I got to know a whole bunch of really cool people and picked up something from each and every one of them. I learned something about handmaking shoes the old way—the styles and designs. And I took that knowledge and started making handmade shoes.”
Rozeske’s shoes are custom fit to her customer’s foot. She traces around the foot and measures it in several places, and then she builds the boot to fit. She cuts out leather and stitches it together, and each of her shoes has two pairs of soles: an insole and an outsole. When the outsole is worn out, she can replace it with a new one.
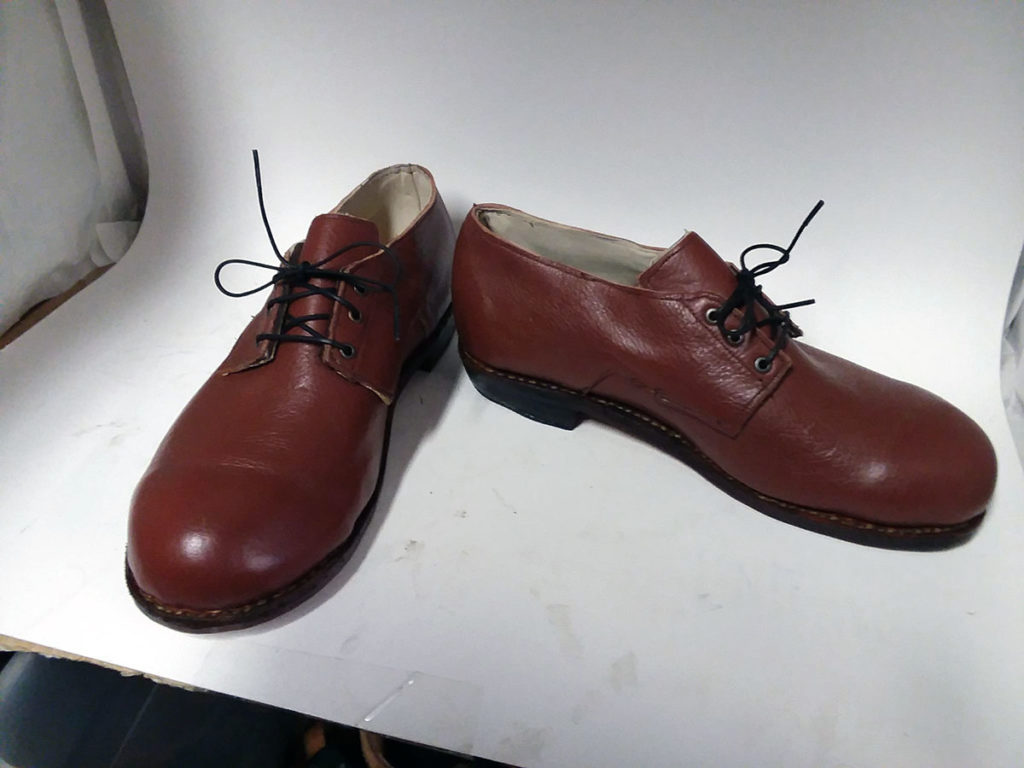
Modern tools
Along the way, Rozeske has added some helpful equipment to her one-woman operation: two stitching machines. She found the first one—a Landis outsole stitcher—in 2004, though it took her quite a while to get the antique machine up and running. The second one, a 1930s Sutton outsole stitcher, was acquired through a grant from the Prairie Regional Arts Council in Waseca in 2019.
“I need to speed up production,” she explained about why she wrote the grant. “There’s a difference between profit and being sustaining. I’m making a profit when I make shoes, but it’s not fulfilling all my needs. I need to speed up in order to do that. I wrote the grant and got the machine as part of getting up to a productive self-sustaining artist, and that is still my aim.”
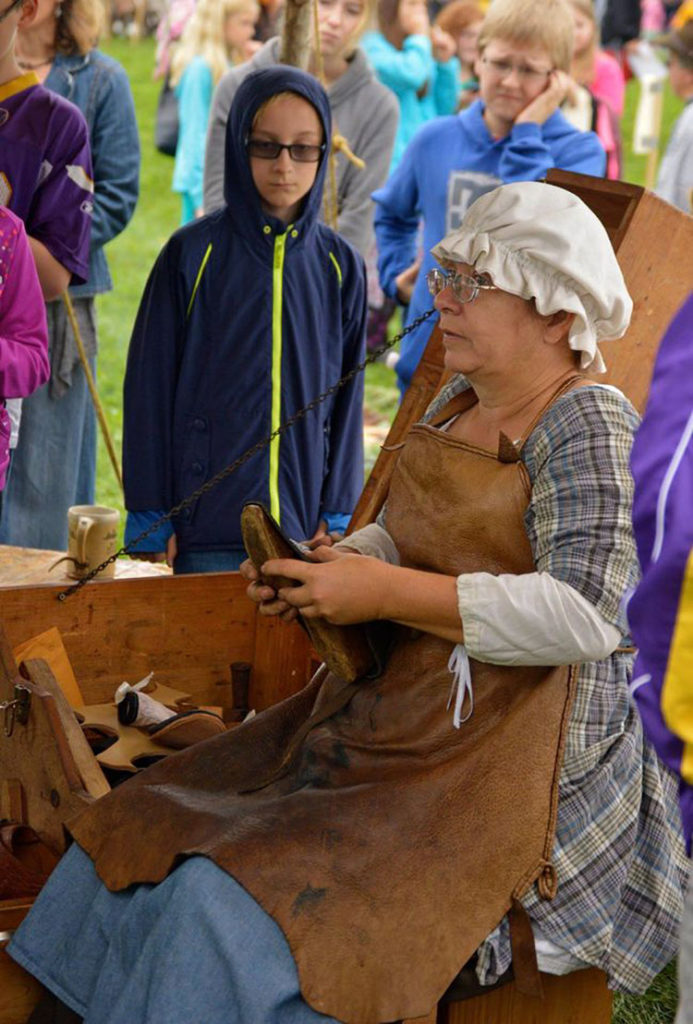
Each machine cuts down her worktime immensely. Rozeske estimated that it takes her two days to finish stitching a shoe’s insole by hand, whereas it takes only 20 minutes with the machine (“and I’m slow, because I’m not proficient yet,” she added). It’s the same with stitching an outsole: 30 minutes instead of a day.
“It takes a lot of hours out of it,” she said.
There’s a difference between being cheap and being inexpensive. It’s cost versus value.Pegeen Rozeske
With these two machines, it now takes Rozeske about three weeks to create a custom pair of boots. She charges by the finished product, with tall boots costing about $425 (more if you want decorative stitching) and brogans (ankle-height boots) costing $145. They’re not cheap, but Rozeske said they’re well worth the cost.
“There’s a difference between being cheap and being inexpensive,” she explained. “It’s cost versus value. My shoes are made to fit your foot. I had one gentleman who wore the boots I made for him this weekend for the first time. He said, ‘I walked around all day and they don’t hurt. There’s no break in. They just fit my feet!’ I said, ‘That was my goal.’ They always seem so surprised.”
She added that leather boots are also a good investment because they’re able to be repaired several times. In contrast, many modern shoes have insoles made of flimsy material, such as cardboard, so they can’t be fixed once they’re broken.
“[My outsoles] are intended to be repaired,” Rozeske said. “When you start wearing through, before you get into the inside sole, you bring it back, and I’ll take that off, put a new one on, stich through the same holes so you can’t even tell it’s been repaired, and you can walk another 100 miles in them.”
Sharing her knowledge
Creating custom footwear—and other leather products—is now Rozeske’s full-time job, but she still finds time to share her love of leatherwork with a new generation. A lot of the time, she’s able to do both at the same time through stints at historical reenactments around the country. She has been as far east as the Erie County Fair in Hamburg, NY, and as far southwest as Phoenix, Ariz. Meanwhile, the time periods represented at these events range from the 1630s to the 1870s.
While at these events, Rozeske wears period-appropriate attire that she has sewn herself and spends her time demonstrating how to make shoes with historic methods. She estimates that she sees about 6,000 school children every fall, mostly at Big Island Rendezvous.
“I enjoy teaching, [and] I enjoy the children,” Rozeske said. “I’ve had them wander into my awning and crawl up on a chair and just sit there and not say a word for hours. They’re excited, and they want to learn.”
Just bring your stuff, and we’ll all work on it together and have a grand old time in the evening.Pegeen Rozeske
Rozeske also used to teach classes ranging from basic leatherworking to shoemaking at the Mankato Makerspace, though many of them had to be canceled earlier this year due to COVID-19. However, she is now able to offer an individual shoemaking course. The course requires you to book four days for a total price of $400, which covers all necessary materials. In this course, Rozeske teaches people how to make an ankle boot. Those interested can find a time that works for them, Rozeske and the Makerspace.
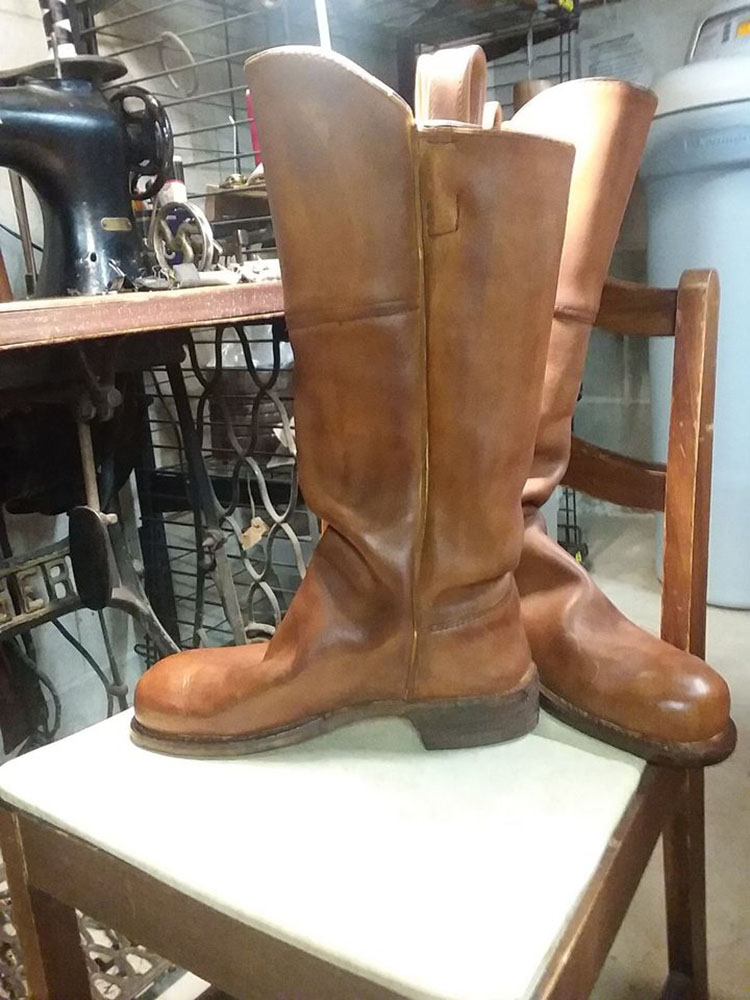
For folks who want to see what leatherworking is all about, or those who just want a little guidance on their current project, Rozeske hosts a weekly “Leather Projects Club” on Tuesdays from 8 p.m.-12 a.m. People can drop in for $15 a night (or $40 for a purchase of four nights) to work on whatever their current project is. They need to bring their own materials, though Rozeske can help them find what they need, and she will them throughout their project.
“You decide what you want to make, and I’ll help you make it,” she said. “You bring your project, and we’ll sit together, and I’ll teach you techniques to [make] whatever it is you want to make: a purse, a wallet, a belt. Everybody works on what they’re working on, and I bring my things to work on. They learn at their own pace, and they don’t have to be here every week. Just bring your stuff, and we’ll all work on it together and have a grand old time in the evening. Come on down to Makerspace. Bring your ideas. We’ll make them work together.”